The growth of AI-driven automation in manufacturing
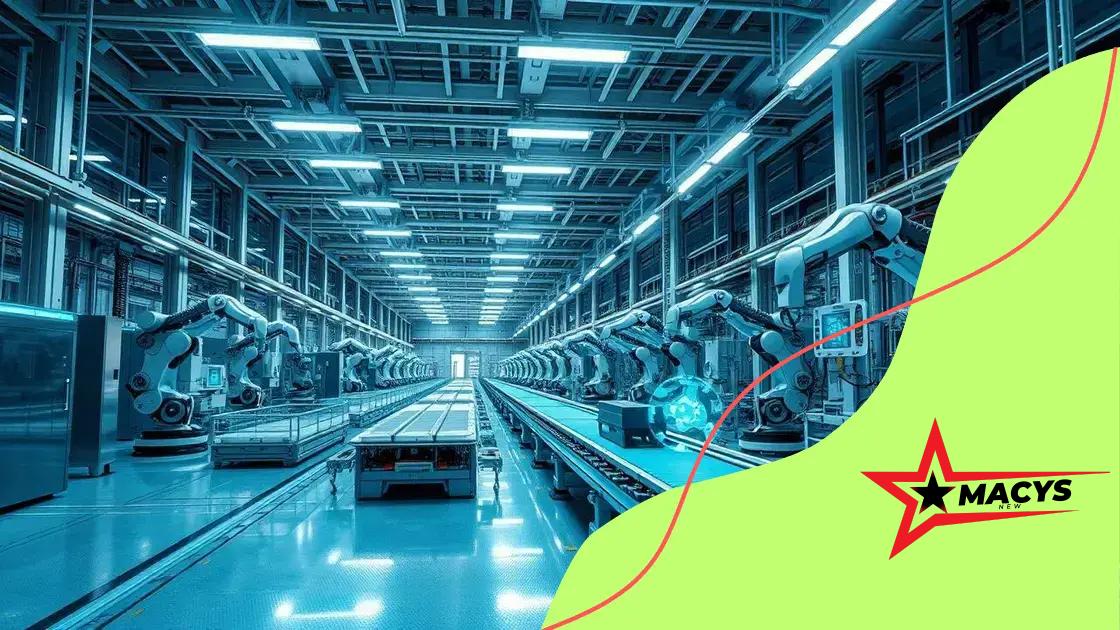
The growth of AI-driven automation in manufacturing enhances efficiency, reduces costs, and leverages advanced technologies like AI, IoT, and robotics to create smarter, more adaptive production environments.
The growth of AI-driven automation in manufacturing is changing the landscape of how products are made. Have you ever wondered how this tech boosts efficiency? Let’s explore its fascinating impact!
Understanding AI-driven automation
Understanding AI-driven automation is essential in today’s manufacturing landscape. This innovation brings together artificial intelligence and machinery, creating systems that can learn and adapt without human intervention.
As businesses strive for more efficiency, they turn to AI to enhance their operations. This technology is not just a trend; it’s here to stay, reshaping how factories function.
Core Principles of AI in Automation
At its core, AI-driven automation relies on machine learning and data analytics. Understanding these principles helps stakeholders grasp how it works.
- Machine Learning: AI systems can analyze patterns from vast amounts of data.
- Real-time Decision Making: These systems make choices based on real-time information.
- Predictive Maintenance: AI predicts when machines need maintenance before breakdowns happen.
The integration of AI into manufacturing can streamline processes. By automating repetitive tasks, workers can focus on more complex problems. This shift not only boosts productivity but also improves job satisfaction.
The Role of Data
Data is the backbone of AI-driven automation. The more data gathered, the more effective the AI becomes. Manufacturers can collect data from their machines, supply chain, and consumer feedback.
- Quality Control: AI helps in identifying defects early in the production process.
- Supply Chain Optimization: AI can adjust production schedules based on demand predictions.
- Customer Insights: Analyzing buyer behavior aids in tailoring products.
Moreover, as more companies adopt AI, they create a competitive advantage. The future is about using technology to not only keep up with the demands of the market but to lead the way in innovation.
AI-driven automation is paving the path for smarter factories. It’s about creating environments where machines and humans work together harmoniously, enhancing production while maintaining quality.
Benefits of automation in manufacturing
Benefits of automation in manufacturing are transforming the industry in remarkable ways. By embracing automation, manufacturers can achieve higher efficiency and flexibility in their production processes.
Automation reduces the time it takes to complete tasks, which directly impacts overall productivity. With machines doing repetitive tasks, human workers can focus on more complex challenges that require critical thinking and creativity.
Key Advantages of Automation
The advantages of automation in manufacturing extend beyond just speed. Here are some key benefits:
- Increased Efficiency: Automated systems operate faster and with fewer errors than human workers.
- Cost Reduction: Lower labor costs and increased output can significantly reduce production costs.
- Consistent Quality: Automation ensures a uniform level of quality by minimizing human errors.
- Enhanced Safety: Dangerous tasks can be automated, reducing the risk to human workers.
As manufacturers shift towards smarter solutions, they discover that automation can enhance their adaptability to market changes. By utilizing data analytics and real-time monitoring, businesses can quickly adjust their production strategies. This kind of agility is crucial in today’s fast-paced market.
Moreover, automation also contributes to sustainability. Automated processes often use less energy and materials, leading to reduced waste. As a result, companies not only save money but also help protect the environment.
The Impact on Workforce
Some worry that automation might eliminate jobs, but it actually creates new opportunities. Workers will find roles that require more skill, such as programming and maintaining automated systems. The shift towards automation means that the workforce can evolve and adapt to new technologies.
Overall, the benefits of automation in manufacturing are vast. By investing in technology, companies can boost productivity, maintain a competitive edge, and create a safer, more efficient working environment.
Key technologies driving AI in factories
Key technologies driving AI in factories are revolutionizing the way manufacturing is done. These technologies help companies increase efficiency and maintain high quality in production processes.
At the forefront of this change are several technologies that enhance productivity and decision-making in real time. Understanding these technologies is crucial for companies aiming to leverage AI for better results.
Artificial Intelligence and Machine Learning
The backbone of automation is artificial intelligence (AI) and machine learning (ML). AI helps machines learn from data, while ML allows these systems to improve performance over time. By analyzing patterns, AI predicts outcomes and enables faster decision-making.
- Predictive Analytics: This technology forecasts future trends based on historical data.
- Computer Vision: AI uses images to monitor quality and detect issues on the production line.
- Natural Language Processing: Helps in analyzing customer feedback and improving product development.
Another critical technology is IoT (Internet of Things), which connects machines and devices to the internet. IoT devices collect data that is used to optimize production. This connectivity leads to smarter systems that can communicate and react swiftly to changes in the manufacturing environment.
Robotics and Automation
Robotics plays a significant role in AI-driven factories. Robots perform repetitive tasks with precision, freeing human workers for more complex activities. This not only speeds up production but also enhances safety by minimizing workers’ exposure to hazardous tasks.
- Collaborative Robots (Cobots): Designed to work alongside humans safely.
- Automated Guided Vehicles (AGVs): Transport materials around the factory floor efficiently.
- Industrial Robots: Handle heavy lifting and increase production speed.
Moreover, the integration of advanced analytics into manufacturing processes allows companies to make data-driven decisions quickly. By examining data in real-time, manufacturers can identify bottlenecks and improve workflows. This adaptability leads to a more responsive production environment.
Overall, the key technologies driving AI in factories are transforming traditional manufacturing into a high-tech industry. As companies adopt these innovations, they position themselves for greater success in the competitive market.
Challenges to implementing AI-driven solutions
Challenges to implementing AI-driven solutions in manufacturing are significant and multi-faceted. As companies seek to integrate AI technologies, they often face various obstacles that can hinder their progress.
One major challenge is the high cost of investment. Implementing AI solutions typically requires substantial upfront costs for hardware, software, and training. Many manufacturers may find it difficult to allocate the necessary budget, especially smaller companies with limited resources.
Data Quality and Availability
Data is the lifeblood of AI, and poor data quality can lead to ineffective solutions. If the data collected is incomplete, inconsistent, or inaccurate, AI systems will not perform correctly. Companies need to ensure they have robust data management processes in place.
- Data Collection: Gathering sufficient data for the AI system to learn effectively can be a daunting task.
- Data Integrity: The accuracy and reliability of data must be maintained over time.
- Data Privacy: Ensuring compliance with privacy regulations while collecting and using data can be complex.
Another challenge is the skill gap in the workforce. Many employees may lack the necessary skills to operate and maintain advanced AI systems. Companies need to invest in training and development to bridge this gap and prepare their workforce for new technologies.
Change Management
Implementing AI-driven solutions often requires significant changes in company workflows and processes. Resistance to change is common among staff who may be uncomfortable with new technology. Effective change management strategies must be employed to help ease this transition.
- Instilling a Culture of Innovation: Encouraging employees to embrace technology is vital for successful implementation.
- Clear Communication: Keeping all team members informed about changes can reduce anxiety and promote acceptance.
- Support Systems: Providing assistance and resources during the transition can help ease frustrations.
Lastly, cybersecurity concerns present another significant challenge. As AI systems become more integrated into manufacturing environments, the risk of cyber-attacks increases. Companies must prioritize cybersecurity measures to protect their systems and data from potential threats. This creates a pressing need for both technological and strategic solutions in tandem with AI implementation.
Navigating these obstacles is vital for manufacturers looking to harness the power of AI. Overcoming these challenges can lead to significant rewards in efficiency, productivity, and competitiveness in the ever-evolving industrial landscape.
Future trends in manufacturing automation
Future trends in manufacturing automation are shaping the future of industry. As technology continues to evolve, manufacturing processes are becoming smarter, faster, and more efficient.
One significant trend is the increased use of artificial intelligence (AI) and machine learning. These technologies are enabling machines to learn from data and improve their performance over time. This shift allows for more adaptive manufacturing systems that can respond to changes in demand or production needs quickly.
Integration of IoT
The integration of the Internet of Things (IoT) will also play a crucial role. By connecting machines and devices to the internet, manufacturers gain the ability to monitor and manage their operations remotely. This connectivity leads to better data collection, allowing for real-time insights into production processes.
- Remote Monitoring: Manufacturers can track performance and detect issues early from anywhere.
- Improved Efficiency: IoT enables automated adjustments based on real-time data.
- Energy Management: Smart systems can optimize energy usage, reducing costs.
Another trend is the rise of collaborative robots or cobots. Unlike traditional robots that operate independently, cobots work alongside human workers. This collaboration not only enhances productivity but also minimizes the risk of workplace injuries.
Advanced Analytics
Advanced analytics will also take center stage in manufacturing. Companies will use big data and analytics tools to predict market trends and customer demands. This proactive approach allows for better planning and resource allocation.
- Predictive Maintenance: Using data to anticipate equipment failures before they happen.
- Market Analysis: Understanding customer preferences to tailor products effectively.
- Resource Optimization: Analyzing data to improve supply chain efficiency.
Furthermore, sustainability will remain a critical focus. As manufacturers look to reduce their environmental impact, automation will enable more efficient resource use. This includes recycling materials and minimizing waste in production.
Overall, the future of manufacturing automation is bright. As businesses embrace these trends, they will not only enhance their operations but also drive innovation in the industry, leading to a more connected, efficient, and sustainable manufacturing environment.
In conclusion, the landscape of manufacturing is undergoing a significant transformation due to AI-driven automation. As companies continue to embrace this technology, they are not only improving efficiency and productivity but also enhancing flexibility and sustainability in their operations. The future trends—like advanced robotics, IoT integration, and data analytics—promise to revolutionize how factories operate. While challenges remain, overcoming them can lead to a truly innovative manufacturing environment. Embracing these changes will be essential for staying competitive and meeting the demands of a fast-evolving market.
\n\n
Aspect | Details |
---|---|
🚀 Efficiency | Automation increases overall production speed and accuracy. |
🌱 Sustainability | Helps reduce waste and improve energy efficiency in factories. |
🤖 Innovation | New technologies lead to innovative production methods. |
👥 Collaboration | Robots and humans working together for enhanced safety. |
📊 Data Insights | Data analytics inform better decision-making in operations. |
\n
FAQ – Frequently Asked Questions about AI-driven Automation in Manufacturing
What are the main benefits of AI-driven automation in manufacturing?
AI-driven automation increases efficiency, reduces costs, and enhances quality control in production.
What technologies are key in AI-driven manufacturing?
Key technologies include artificial intelligence, machine learning, IoT, and advanced robotics.
What challenges do companies face when implementing AI solutions?
Challenges include high costs, data quality issues, skill gaps in the workforce, and change management.
How will automation affect the workforce?
While some jobs may change, automation can create new opportunities for more skilled roles in technology and management.